This article is from ECHO Asia Note # 35.
Introduction
One of the best things that you can do to complete your sustainable farm or garden is to balance it with a small livestock unit. Livestock integration is fundamental #10 in my book Sustainable Agriculture in the Tropics. If you read ECHO Asia Notes, chances are good that you are involved in some way in farming or gardening. Livestock will produce low cost, high quality fertilizer, while also yielding food to eat or clothing material to wear. Although scientists have attempted to replicate the benefits of traditional integrated livestock systems, the quantified results are not always easy to show in field trials.

Figure 1: A drought tolerant bovine grazes humidicola grass (Brachiaria humidicola) under well-spaced coconut in the Philippines. Integrating cows in this way saves on grass cutting chores and other costs common in the industry.
On the Aloha Farm in Puerto Princesa, Philippines, we calculate that our hogs typically bring in a net profit of $30-40 USD per head. With 12 to 15 units in a staggered harvest, they have the potential of bringing in 200-300 USD profit per quarter. In addition, we started using 20-liter pails to measure the volume of manure from the hogs, and found that manure production was over 25 m³/quarter for a batch of 12 to 15 hogs. The manure composts down to 10 m³/quarter, which is enough to fertilize a hectare of sweet corn—earning us $300 USD profit.
Beyond that, we found that the crop residue from the corn stover could be made into biochar, fed to goats, or composted with more hog manure to continue the cycle. We are much more diverse than most farms, but I hope this example helps you begin to see the value associated with an integrated crop-livestock model. The animals on your farm have tremendous potential to increase the fertility of the overall system without the need for expensive external inputs (Figure 1).
Traditional Integrated Systems
According to the Food and Fertilizer Technology Center (1999): “Farmers tend to integrate livestock and crop production better than most scientists do!” We can learn a lot from these existing systems and their years of trial and error (FFTC 1999). Sajise points out that “Traditional systems already combine various mixtures of livestock species and crops. The challenge is to increase the productivity of traditional systems, so they may produce higher [amounts of] usable biomass while conserving the natural resources on which the whole agricultural system depends” (FFTC 1999). According to the International Rice Research Institute (IRRI), in regions such as Asia, mixed crop-livestock systems can probably be regarded as the foundation for the production increases that improved food security and helped alleviate poverty (Sombilla and Hardy 2005).
Paris (1992), summarizing the results of rice-based crop- livestock farming systems research in the Philippines and other Asian countries, enumerated crop-animal interactions as follows:
- Use of animal power in crop production, transportation, and processing; and use of crop by-products (straw, bran, and residues) by livestock and poultry.
- Use of animal manure to improve land productivity and cut input costs.
- Minimizing production risks by combining crop and livestock enterprises.
- Small-farm household consumption of milk, meat, and eggs, thus substantially improving human nutrition and health.
- Sale of livestock and poultry and their products to improve and stabilize farm income for the purchase of cash inputs and to offset household expenditures, such as school fees, social obligations, and health care.
However, the main issue in crop-animal interactions is the lack of methodology for measuring the benefits derived from them.
Getting Creative with Integrated Crop-Livestock Options
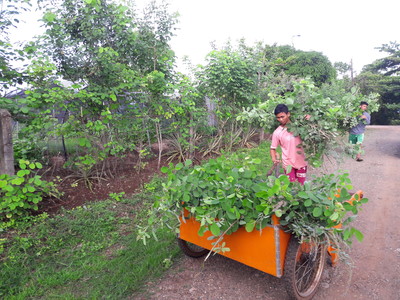
Figure 2: Efficient daily harvest of cut-and-carry legumes for goats, cows, and hogs will reduce feed costs
Properly managed livestock can bring the tropical farmer higher profits than some market vegetables and most grains. In permaculture, we say “integrate instead of segregate!” An example of this is the way farmers integrate their grazing livestock into seasonal cropping patterns. In traditional upland farmland systems, cattle and goats are left to graze in the forest or taken up onto higher ground away from the cropland during the growing season. When the harvest is over, the animals are brought back to the village to graze on the fallow croplands during the dry season (FFTC 1999). At the Aloha House Farm, we raise and integrate goats, chickens, ducks, cattle, and hogs (Figure 2). For example, our goats graze pasture and browse as well as feed on legume shrubs, and we feed some crop residues to the goats. With the integrated system, we are able to eliminate many feed costs and (with the manure we collect) also eliminate many fertilizer costs (Figure 3). We cut and carry fresh feed stock for goats, cows, chickens, and hogs; it requires labor, but we are able to minimize inputs.
At the Aloha House Farm we recommend that you allow animals to graze, if space allows. However, this is not always feasible in smallholder settings or urban environments. Where grazing is not an option, you can use various grains as supplemental feed. Consider fermenting the grains with beneficial microbes to increase feed conversion; we find that the fermented grains also act as probiotics, minimizing the need for medications.
Omnivores such as hogs, chickens, and ducks also do well with some silage sources (we use Effective Microorganisms (EM) to initiate our fermented feeds). The live microorganisms in EM synthesize natural vitamins and make available health-enhancing components that can protect livestock. For us, the EM costs are far less expensive than antibiotics and vitamin shots would be; and have even enabled us to remove the need for any antibiotics in our system. We spray all pens and barns weekly with EM to minimize odors and flies. The high number of beneficial bacteria begin to exclude pathogens through competition. According to Higa and Parr (1994) EM-1 is a commercially available blend that contains three types of microorganisms:
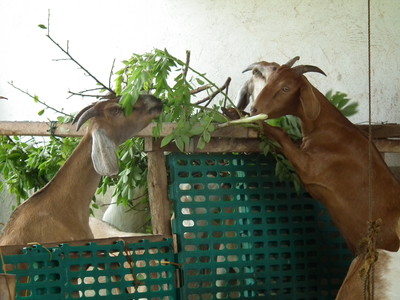
Figure 3: Gliricidia and leucaena fed on racks to goats.
- Lactic Acid Bacteria - This family of bacteria are also used to make yogurt and cheese. The bacteria convert sugars into lactic acid. In the process, they lower the pH, inhibiting the growth of pathogenic microbes and make it difficult for methane-producing microorganisms to survive.
- Yeasts - These are single-celled fungi such as those used in making bread and alcohol. They kick off the process of fermentation.
- Photosynthetic Bacteria - These bacteria allow the other microbes in the mix to coexist. They use photons to metabolize organic and inorganic substances. According to Drs Higa and Parr, (1994) the photosynthetic bacteria “perform incomplete photosynthesis anaerobically” (i.e. in the absence of oxygen). Since the process of photosynthesis yields oxygen as a byproduct, these bacteria help provide oxygen to plant roots. Photosynthetic bacteria are also beneficial for their ability to detoxify soils, for example by transforming substances like hydrogen sulfide into useful compounds, and for their ability to fix nitrogen.
As part of our animal feeding system, we cut and carry daily. We feed the goats in their enclosures until the sun dries the pasture, making it safer for them to graze; in our area, parasites infect the rumen when goats graze on wet grasses. We feed the bucks, kids, and does from our established fodder banks and contour hedgerows of Tick-trefoil (Desmodium rensonii), Malabalatong (Flemingia congesta), (Indigofera), Kakawate or Madre de Cacao (Gliricidia sepium), Ipil-ipil (Leucaena leucocephala), and Acacia (Mangium acacia). Sometimes our goats even eat some of the bark. Please refer to AN #31 Ruminant Feeds for more information.
As they eat, a small herd of goats can create huge piles of leftover sticks and branches that can be dried and used for cooking fuel. This practice of cut and carry combines gathering feed for the goats with the daily chore of scavenging for fuel, demonstrating another great benefit of integrating livestock on the farm. Although it can be difficult to quantify the economic value of feed and fuel, you will find your labor time reduced by acting in intentional ways.
By properly composting biomass on the farm, we increase our production of grains, vegetables, and herbs, reducing fertilizer costs and increasing yields. This is the main benefit in our system in the Philippines, but we will explore other benefits as well, including the production of biochar from waste.
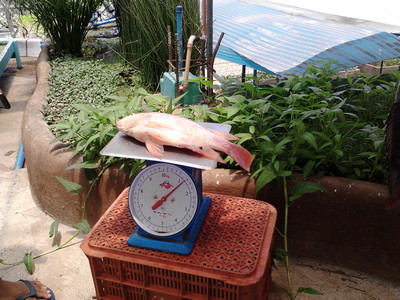
Figure 4: In this aquaponics system, fish and plants are reared separately but are linked together in a closed loop water recirculating system. With the help of beneficial microorganisms and proper design, the fish fertilize the plants and the plants filter the water for the fish.
Integrated Aquaculture and Plants
In addition to the cut-and-carry systems we use for our larger livestock, we have experimented heavily with a scaled down monogastric fish production system adapted for aquaponics where we raise tilapia. Ducks also participate in the aquatic system by swimming, foraging, and bathing in designated ponds linked via plumbing and recirculating water but not containing the fish crop. We use the wastewater for simultaneous vegetable production (Figure 4). Please see ECHO Asia Note 20 for more information. Not all farmers succeed with this kind of system, so if you experiment, begin with caution and on a small scale. For example, Little and Edwards (2003) warn of the failure of scaled-down modern systems integrated with aquaculture. “Small-scale, feedlot monogastric-fish systems have been shown to be technically viable in on-station and researcher-managed, on-farm trials. However, sustained adoption of these types of systems by farmers has been rare” (Little and Edwards 2003). You can think of any livestock system that is confined and dependent on mainly purchased input as a “feedlot” regardless of size. The economy of scale can make small operations unsustainable because of the low profit margins and cost of purchased inputs.
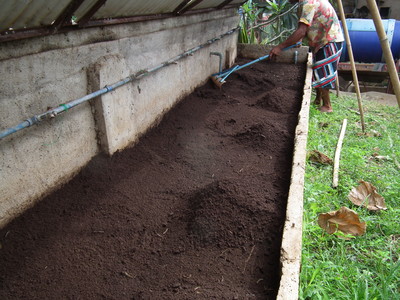
Figure 5: Top Harvest Vermicasts – weekly castings are top harvested until ½ of the composted manures are depleted. Then, two-week old hot EM composted manures are added to the vermiculture bed.
Vermicompost Production
Using manure from our animals, we have integrated the production of vermicompost into our agricultural system (Figure 5). Our worms are fed pure composted manure from the cattle, goats, and hogs. The resulting vermicasts are mixed into potting soil for use in our nursery (our potting soil is made with 20-25% pure vermicasts). This critical part of our herb and vegetable production has always been worth the added management. We can harvest 6-10 liters of vermicast per m² using African night crawler worms (Mikkelson 2015). Other projects throughout the tropics have also integrated this manure-vermicomposting approach, including the Mindanao Baptist Rural Life Center in the Philippines (Tacio 2014; Capuno 2010).
Managing Nutrient Cycles

Figure 6: This Heifer Thailand biogas unit at Aloha House, Philippines, is a floating drum digester
When farmers begin to integrate livestock with crop production, the animals’ waste will increase yields the most. In our system, only manure in barns and night-time enclosures is gathered and mixed with other materials for compost. Manure from penned animals is easy to collect. For grazed livestock, any manure in our rotational grazing systems stays in the field to fertilize the pasture and contribute to the ecosystem stability. The manure will be incorporated by microorganisms, beetles, earthworms etc. without any further human intervention. We have copious amounts of manure available from our barns, and need not spend the additional time and effort in the field gathering manure. If you are just getting started and in need of manure for composting, you may decide to gather what you can. However, in the future you will want to find a way to collect manure in the livestock enclosures, in order to conserve time and labor.
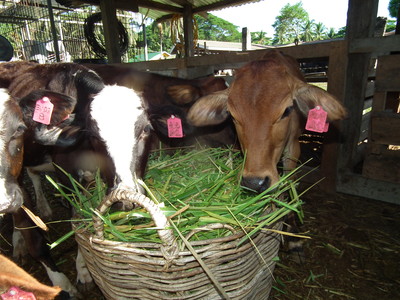
Figure 7: In Thailand, dairy cattle co-op members share resources and grow napier grass and legumes and also sell silage to each other. The manure is used for fertilizer.
If you want to convert a feed-lot type enterprise into something more sustainable and you wish to use more of the on-farm resources, you will need to find ways to use the waste stream (Figure 6). Above are some estimates of manure production for several types of systems. Heifer Thailand has a well-designed biogas unit that can use liquid manure to produce methane for heating/cooking (Meyers 2012; Figure 7). ECHO has other options for biogas digesters, available on www.echocommunity.org. For example, see a presentation by Wilkie (2016) and other resources at https://www.echocommunity.org/en/search?q=biodigesters

Figure 8A: When hot composting tropical manure, crop residue, and weeds, temperatures should rise from 25-30º C in the beginning of the composting cycle to >60º C, in order to safely eliminate pathogens and disease.
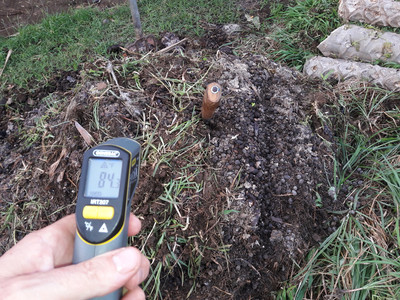
Figure 8B: Measuring temperature inside a working compost pile.
On our farm, we always compost our manures aerobically to generate the heat that eliminates pathogens and diseases. Aerobic composting, or “hot composting,” allows certain universal thermophilic microorganisms to break down the organic waste into usable, stable compost. Temperatures above 60ºC in your compost pile will kill weed seeds and pathogens (Richard 1992). Monitor the temperature daily until you get a feel for it. Place a machete or metal rod (Figure 8A) into the core of the compost pile for 10 minutes. After you pull it out, use an infrared thermometer to read the temperature of the metal (if you use your hands, it should be uncomfortably warm to the touch) (Figure 8B). We turn our compost piles once a week for a total of three weeks. You can read more about compost in my book, in the chapter on Fundamental #4: Composting.
The Added Step of Biochar Production
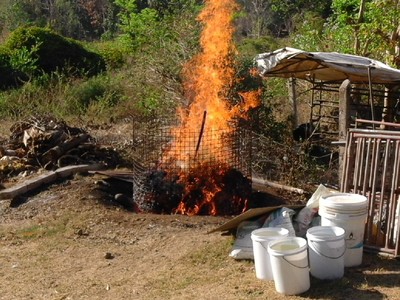
Figure 10: To minimize water consumption during the dry season, water is already in position to douse and “activate” the corn stover in a pyrolizing cage over an earthen pit.
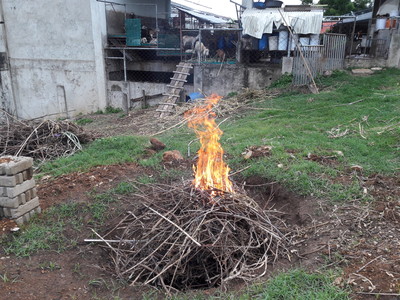
Figure 9: Cut and carry sticks and branches are dried after the goats eat the leaves. Once dried, the woody material is efficiently converted into biochar by top lighting the pile.
To take your soil management to the next level, consider utilizing woody waste materials and husks for biochar production. Through a controlled process called pyrolization (from the Greek, meaning fire separating) you can convert the woody carbon matter (lignin) into a highly porous, nutrient-holding, biologic powerhouse and soil conditioner. We dry the sticks and branches from our cut and carry goat feed waste, and pile them in a circle around a centralized pit (Figure 9). When the sticks are adequately dried of water vapor, we top light the pile. Place your kindling and dry paper or grass on the top of your stack and light from the top. Airflow will be drawn in from the bottom of the pile and preheat on the way up through the coals as they burn downward. This increases efficiency and gives a higher yeild of biochar. If the sticks are compressed, the pit will not allow airflow from below and block air from the bottom. We use dried Cogon imperica grass as an accelerant to ignite the top of the pile, thus igniting the Top Lit Up Draft (TLUD) biochar system in the pit. The TLUD process burns the combustible oils and gases while minimizing smoke and producing a clean burn. A migratory pyrolytic front efficiently works its way down the pile and is doused with water to harvest the char before allowing it to become ash (Figure 10). Some trial and error is required before you know when to stop the burn—you need to stop it before all of the wood is converted, and not allow it to burn to ash. We have a permanent pit surrounded by various piles of sticks drying at different stages (the leftovers of our cut and carry for our goats; Figure 11), and have found that we require no clunky, rusting metal retorts or machines.
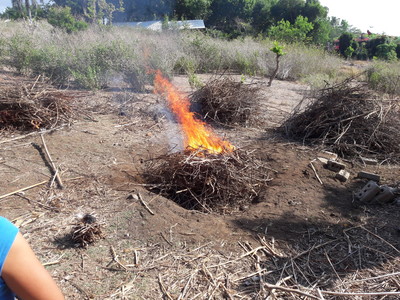
Figure 11: Sticks are piled in weekly batches to ensure uniform drying. They are TLUD pyrolized when moisture content is 20-30%. When there is moisture content of 20-30%, sticks will be brittle or crisp, when you bend them they crack and look dry with no green layers. Also if you see the stick bark blistering and bubbling on the end when you pyrolized them, they are too high in water content. At 20-30% MC the residual moisture is mainly comprised of oils, not water, which aids in the conversion of the lignin, cellulose, and hemicellulose from the woody material into char without becoming ash.
Biochar can also be made from other forage crop residues, such as corn stover or napier grass (Pennisetum purpureum), but stacking is difficult without a cage. We use steel matting formed into a cylinder to form a TLUD pyrolizing cage. We also pyrolize old coconut husks into a nice crumbly biochar that works well in our raised beds for herbs and vegetables.
Activating and Charging Biochar
Biochar can be made through many different methods, but the farmers we work with are most concerned with ease of operation and efficiency. However you make it, you should “activate” the biochar, and charge it with nutrients and microbes. We activate biochar by dousing it with water at the end of the production cycle. Water saturation activates the charcoal by attaching electrons so as to prevent the biochar from tying up nutrients in the soil. According to Craggs (2017), for biochar to have an immediate beneficial effect it must first be subjected to a process of “activation” (also termed inoculating or charging). Once activated, and subsequently charged with high levels of essential nitrogen and phosphorus, the many micro-fauna naturally establish, develop and grow in the maturing biochar compounds.
We also add biological and nutrient inputs, so that the biochar will not lock up the soil nutrients when we add it to the soil. We charge biochar with EM, compost tea, rich pond water, or fish silage. When needed, we also add mineral rock powders to supply trace elements and limestone for calcium. For more information, please see McLaughlin (2016).
There is some debate as to how long you should age biochar before use. Ranges from days to years are discussed but more research is needed. One researcher actually tested samples over a 15 month range and found higher CEC (Cation Exchange Capacity) in biochar after 15 months of field-aging. Overall, the 15 month field aging only had a significant effect on biochar pH and nanopore surface area, both of which decreased, while CEC increased (Mukherjee et al. 2014). We have found that, after activating and charging biochar, you can utilize it within days, but you may also bag it and stack it for future use; it can store for years. Don’t be alarmed if you find various visible white molds colonizing the char. They should all be beneficial, if you used good quality compost or EM1 to charge your biochar. Check out my slide show on Biochar Options if you want to learn more (Mikkelson 2010).
Making Use of Locally Available Waste By-Products
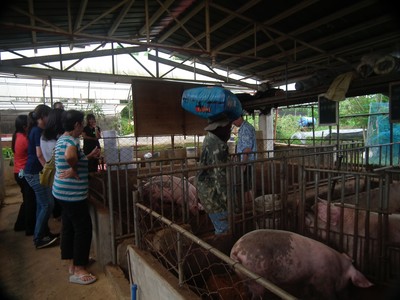
Figure 12: Eco-tourists are always surprised to visit our no-wash, odorless hog pens. Most people do not know that hog production can be an enjoyable, environmentally healthy practice. Eco-tourists are always surprised to visit our no-wash, odorless hog pens. Most people do not know that hog production can be an enjoyable, environmentally healthy practice.
To fully integrate your agricultural system, and to increase production and lower the costs of purchased inputs, look for ways to transform waste products into usable by-products. To fatten hogs, we feed them rice bran, fishmeal, and copra meal fermented in EM. Feeding crop residue to swine lowers our feed costs—a great benefit of livestock integration. We use sawdust beddings, to minimize stress and to allow natural rooting instincts that cannot be practiced on conventional cement flooring; the EM-treated sawdust bedding also helps minimize odors and flies (Figure 12). Our system is a no-wash operation; hogs maintain cleanliness when allowed 2 m² each at the finishing stage (50 kg and up). There is no need to waste water or labor by hosing the hogs down twice a day. We also avoid smelly lagoons of effluent this way.
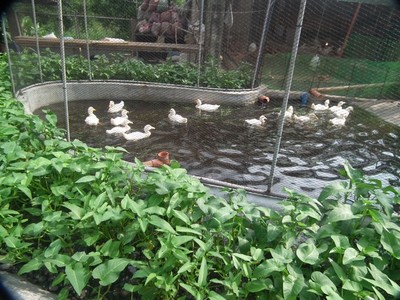
Figure 13: Pond water from our duckponics system is used to grow feed for other livestock.
The hogs’ manure production is plentiful, and it makes great fertilizer when properly composted. We harvest the manure daily and never remove the bedding, so the bedding gets more stable over time as the beneficial microbes colonize the bedding material. We do need to top up the bedding from time to time, because a small amount decays or leaves the system when we harvest the manure. Our hog fattening has been the most profitable of all our livestock units but we still maintain biodiversity within other livestock units (Figure 13).
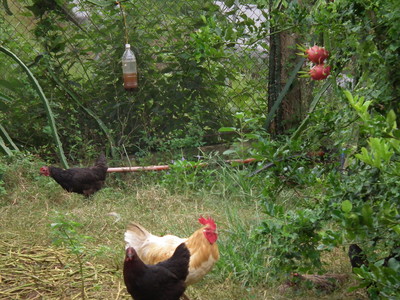
Figure 15: Chickens eagerly forage for maggots from the fallon over-ripe fruits underdragon fruit plants, eliminating fly problems.
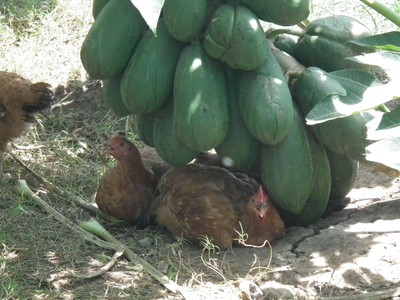
Figure 14: Chickens find shade while scratching and grazing the grasses in a papaya orchard.
Our free-range chickens eat small amounts of corn, sorghum, rice bran, copra meal, azolla, and duckweed, all fermented with EM1. The laying hens get crushed limestone as well as a calcium supplement. We give our chickens plenty of room to graze and scratch, and water is always available (Figures 14 and 15). The chicken enclosure has a bedding made from natural components, similar to the sawdust bedding of our swine systems. However, we use up to 50% rice hull and about 5% charcoal to stabilize the manure. We inoculate (spray) the bedding with EM1; the beneficial microorganisms keep the environment healthy for livestock, reduce odors and minimize the number of flies. We never completely empty the bedding from poultry. At most we harvest 50% of the bedding and then mix in more fresh bedding materials. A mature bed is biologically stable and will provide a safe indoor habitat indefinitely if managed properly. If we removed all the bedding, the beneficial microorganism populations would have to start populating the bedding all over again. We have found that fresh bedding is not stable, and disease can be an issue in the beginning.
Conclusions
Integrated livestock systems can provide many benefits (Tables 2 and 3). With careful planning and by starting small, most farmers will be able to incorporate cows, goats, chickens, or hogs and improve the stability of their farm. Crop residues can reduce feed costs, and manure can reduce fertilizer costs. Manure can also be used to produce biogas for cooking or heating, to reduce costs on the farm. Grazing livestock can help manage weeds and improve soil health. With efficient management, you can turn even the waste stream from cut and carry feeds into the useful by-product of biochar. The key is to take on one appropriate technology at a time and to look for ways to minimize labor. Soon you will be able to safely expand as you adapt and apply lessons learned. Then you will be able to share with other farmers in your area!
Table 1: Common Livestock Manure Sources and Nutrient Estimates (NRCS 1995).
Table 2: Profits from Animal Integration into Agroecosystems (Carpenter-Boggs et al. 2013).
Table 3: A Summary Table of Some of the Many Benefits of Crop-Livestock Integration (Kersbergen 2008).
REFERENCES
Carpenter-Boggs, L., K. Painter, and J. Wachter. 2013. Integrating Livestock in Dryland Organic Crop Rotations. Extension eOrganic Webinar. Presented October 22, 2013. Available: http://eorganic.info/sites/eorganic.info/files/u461/DrylandLivestock.pdf
Capuno, J. V. 2010. Earthworm castings getting popular as organic fertilizer. Edge Davao. Available: http://edgedavao.net/agritrends/
2010/08/23/earthworm-castings-getting-popular-as-organic-fertilizer/
The Compost Gardener. 2008. EM-1 Effective Microorganisms. Available: https://www.the-compost-gardener.com/em-1.html
Craggs, G. 2017. Activated biochar to enhance soil productivity and mitigate global warming. Future Directions International. Available:
http://www.futuredirections.org.au/publication/activated-biochar-enhance-soil-productivity-mitigate-global-warming/
[FFTC]. Food & Fertilizer Technology Center. 1999. Integrated Crop-Livestock Production for the Slopelands of Asia. Retrieved
February 21, 2018. Available: http://www.fftc.agnet.org/library.php?func=view&id=20110729141456
Higa, T., and J. F. Parr. 1994. Beneficial and Effective Microorganisms for a Sustainable Agriculture and Environment. Atami, Japan:
International Nature Farming Research Center. Available: http://www.em-la.com/archivos-de-usuario/base_datos/Beneficial%20and%20
Effective%20Microorganism%20for%20a%20sustainable%20agriculture%20and%20environment.docx.
Kersbergen, R. 2008. Livestock. Midwest Organic and Sustainable Education Service. [MOSES]. Retrieved February 21, 2018. Available:
https://mosesorganic.org/farming/farming-topics/livestock/integrating-livestock-with-crop-production/
Little, D.C., and P. Edwards. 2003. Major types of integrated systems in Asia. In: Integrated Livestock-Fish Farming Systems. Rome:
FAO. Available: http://www.fao.org/docrep/006/y5098e/y5098e04.htm
Meyers, L. 2012. Build Your Own Biogas Digester. Heifer Project International. Available: https://www.heifer.org/join-the-conversation/
blog/2012/May/build-your-own-biogas-generator.html
McLaughlin, H. 2016. An overview of the current biochar and activated carbon markets. Biofuels Digest. Available: http://www.biofuelsdigest.com/bdigest/2016/10/11/an-overview-of-the-current-biochar-and-activated-carbon-markets/
Mikkelson, K. 2010. Low Tech Methods for Making Biochar. Retrieved February 21, 2018. Available: https://www.slideshare.net/
mik1999/char2
Mikkelson, K. 2015. Poster Presentation: 282 Week Study of Vermicast Production in the Philippines. The 2015 ECHO Asia Agriculture
& Development Conference. Chiang Mai, Thailand. Available: https://www.researchgate.net/publication/279517058_282_Week_Study_
Of_Vermicast_Production_In_The_Philippines
Mukherjee, A., A. R. Zimmerman, R. Hamdan, and W. T. Cooper. 2014. Physicochemical changes in pyrogenic organic matter (biochar)
after 15 months of field aging, Solid Earth 5:693-704. Available: https://doi.org/10.5194/se-5-693-2014, 2014.
[NRCS]. Natural Resources Conservation Service. 1995. Animal Manure Management. RCA Issue Brief #7; December 1995. Available:
https://www.nrcs.usda.gov/wps/portal/nrcs/detail/null/?cid=nrcs143_014211
Paris, T. R. 1992. Providing a framework for gender impact assessment of CIAP’s technologies and identifying strategies to address
gender issues in CIAP’s research and training activities. Cambodia-IRRI-Australia Project. Phnom Penh, Cambodia.
Richard, T. L. 1992. Municipal Yard Waste Composting: An Operator’s Guide. A Series of Ten Fact Sheets. Ithaca, New York: Cornell
Resource Center. Available: http://compost.css.cornell.edu/Factsheets/FactsheetTOC.html
Sombilla, M. A., and B. Hardy (Eds). 2005. Integrated crop-animal systems in Southeast Asia: current status and prospects. IRRI
Limited Proceedings No. 11. Los Banos, Philippines: International Rice Research Institute. Available:http://books.irri.org/LP11_content.
pdf
Tacio, H. D. 2014. Learn by doing at Rural Life Center. Davao Sun Star. Available: http://archive.sunstar.com.ph/davao/business/
2014/08/17/learn-doing-rural-life-center-360326
Wilkie, A. 2017. Oral Presentation: The Basics of Biogas for Smallholder Farmers. The 2017 ECHO International Agriculture Conference.
Fort Myers, Florida, USA. Available: https://www.echocommunity.org/en/resources/02917925-06e0-4b35-8dc2-fa78a67d6f58