Introduction
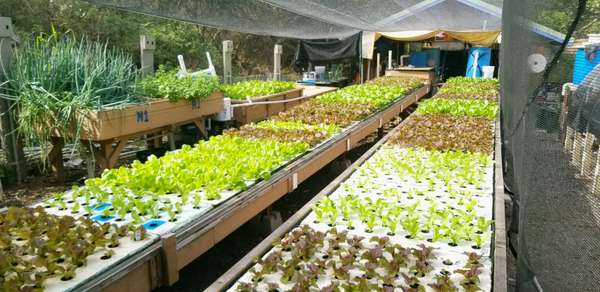
Water pumps have long been a key component of the small-scale farm and are valuable labor-saving devices that offer a variety of practical applications. Pumps of different types are regularly used for water storage & filtration, irrigation, aquaculture systems, and more. While convenient and useful, pumping water does come at a cost – from the necessary consumption of energy, to the regular maintenance of moving parts. However, new developments in appropriate pump technologies offer options that can save money, increase reliability, improve longevity of equipment, and offer certain other benefits that to be presented in this article.
What is an Airlift Pump?
A conventional water pump uses mechanical rotation to directly pressurize and move water. In contrast, airlift water pumps take advantage of the relatively lighter density of air to lift water. Until recently, airlift pumps were only good for lifting water 10 - 15 cm at most, however Glenn Martinez from Hawaii has since shared with the international community easy-to-build designs that can readily lift water 2 to 3 meters in height. In certain configurations, these airlift designs can lift water much higher, even as high as 30 meters out of a subterranean well. This article will focus on just one of his fundamental configurations, referred to as the ‘pipe-in-a-pipe’ airlift pump (Figure 2). This configuration has been used most often to lift anywhere from 400 to 2000 liters of water per hour to a height of 1 to 4 meters, making it a very useful technology for a wide array of systems. As readers will note, this technology brings particular benefits to aquaponics systems, which is the intended use of these particular designs.
The ‘pipe-in-a-pipe’ airlift pump takes advantage of the fact that air injected underwater will expand as bubbles as it rises to the surface, with a 10% increase in volume from a depth of 1 meter. By confining the bubbles inside of a small diameter vertical pipe, these bubbles will act like a piston, or a syringe plunger, lifting portions of water upward as they rise. The physics involved would fill many technical papers, but the net effect is a strong upward current of water and air. The Martinez design works on the theory that larger bubbles, rather than a cloud of small bubbles, are most efficient at lifting water.
The Story Behind the Innovation
Glenn Martinez, the innovator behind the ‘pipe-in-a-pipe’ configuration of the airlift pump, has been involved for many years in teaching, designing, and building of aquaponics systems at his Olomana Gardens farm in Hawaii, as well as internationally in development settings. He also regularly consults on aquaponics project designs, and several years ago was designing an aquaponics system for a local school where it was going to be expensive to supply electricity. To make the system more affordable he invented (or as Glenn likes to say ‘rediscovered’) a way to lift the water from the fish tank up to the aquaponics grow bed with an innovative air pump configuration. Instead of running electrical conduit in a deep trench across the schoolyard, all that was required was a shallow ditch for the air pipe, quickly dug by the students. In the ditch, a 1-inch PVC pipe was installed, connecting the system to the small 60-watt air compressor located across the way in a lockable classroom. As it turned out, the airlift pump that Glenn came up with had multiple advantages for aquaponics systems and other situations where inexpensive and reliable methods of lifting water are needed.
Advantages of Airlift Pumps
Safety
As the story above illustrates, a conventional water pump requires that electricity be located close to the water source. Electricity and water, as we well know, can be a dangerous combination, especially where children are present. Safety, in regard to electricity in water, should be mitigated and taken seriously in any setting. The Times of India reported that as many as 30 people are killed every day in India by electrocution. One intern working on our projects in the Philippines recently asked us for advice when he was shocked twice with a conventional pump; he simply didn’t have much experience working with electrical devices, including how to arrange extension cords so they remained dry in the rainy season. Ground fault interrupt (GFI) circuits, if they are available, can decrease risk but tend to trip at inconvenient times and require monthly testing. As an alternative, the compressor for an airlift pump can easily be set up at a safe distance from the water to eliminate this potential hazard, decreasing risk substantially. Community development workers may find this particular feature of airlift pumps to be especially beneficial for promoting safety.
Aeration of Water
One of the great advantages of an airlift water pump is its ability to aerate water as it lifts it. This can be a highly beneficial feature when incorporated into fish production systems, or other scenarios where water quality conditions will benefit from more dissolved oxygen. In some small-scale aquaponics systems with low fish stocking density, the airlift pump alone will provide enough dissolved oxygen to supply the needs of the fish. Used along with a conventional aeration pump and airstones, an airlift pump can provide extra dissolved oxygen and security against the loss of fish from low dissolved oxygen levels.
Reduced Maintenance & Increased Reliability
Submersible water pumps and conventional external pumps are prone to clogging and need periodic cleaning including disassembly. Additionally, the sand and grit that they draw in will eventually wear out components, often necessitating replacement of the pump. The Martinez airlift pump design will not only handle small abrasives but debris nearly as large as the diameter of the inner pipe (1 to 1 1/2 inches). This means that small fish, clumps of algae, uneaten fish food, etc. are simply carried up and out through the pump. In one of our aquaponics systems, we conducted a trial in which we dumped 20 kg of coffee grounds into a tank to test the ability of the airlift to function without clogging; impressively, it passed through with no challenge. The ability to handle gravel and other debris is demonstrated in this video by Glenn.
At the same time, the air compressor, the most expensive component of the airlift pump, is immune to anything about the water. Freshwater, saltwater, and sludge-laden water are all the same to this pump, as it sits separate from the water source. Additionally, in the case that a conventional submersible pump empties the tank, it will quickly suffer permanent damage from overheating – an air compressor in an airlift pump will just keep on running, ready for the water to return.
Diaphragm air compressors, which are ideal for airlift pumps, are also very easy to repair. Typically, all it takes is a screwdriver to replace diaphragms that wear out every few years. This is simple and much less expensive than replacing an entire conventional pump. Also, changing or moving a compressor can be as easy as unscrewing and reattaching a garden hose.
Other Advantages of the Airlift Pump
In some locations, a water pump is vulnerable to theft or vandalism. Since a 1-inch PVC pipe or length of larger diameter hose offers very little resistance to airflow, an air compressor can be located at a distance, locked separately in a building or storage box.
Airlift pumps may also save money by using less electricity. We replaced one 200-watt submersible pump with an 80-watt air compressor to run an airlift. The lower power requirement makes a solar panel powered system more feasible. Glenn has configured conventional pump systems with air injection to make dramatic cuts in the cost of lifting water 8-10 meters high. We don’t have any experience with it yet, but we’ve seen that DIY airlift pumps can also be configured to pump subterranean wells where the resistance to blockage and ease of repair characteristics would be especially valuable.
‘Pipe-in-a-Pipe’ Airlift Pump Design
Larger volume airlift systems are possible and can be accomplished with different sized air compressors with appropriately sized pipes. Our 110-volt compressors range in size from 35 to 110 watts. Compressor selection is determined by several factors including the height the water needs to be pumped and the desired water output volume. The typical aquaponics ‘pipe-in-a-pipe’ configuration only needs an air compressor capable of generating an initial 5 psi (35 kPa) then be able to run continually at around 2 psi (14 kPa). The compressors that run our aquaponics systems produce in the range of 30 to 100 liters of air per minute. You can see from the chart below that the final water volume output of the pump depends not only on the size of the compressor but several other variables (Table 1). The 100 L/min compressor doesn’t deliver the most water because it is pumping higher out of a shallower well.
We aim to turn over the volume of our fish tanks at least once every two hours and these pumps have been more than adequate for that. Pond supply stores or larger aquarium supply outlets may carry the preferred diaphragm style compressors (or alternately, piston air compressors) for this application.
Critical Design Considerations
The Intake Pipe
In describing one of the key feature of the ‘pipe-in-a-pipe’ configuration, Glenn Martinez had the following tip:
“The latest version of the ‘pipe-in-the-pipe’ configuration does away with drilling many small holes. The conventional wisdom was that the many tiny air-bubbles displaced the density of water, thus the lighter water ‘floated up’. However, on a recent trip to the Philippines we did not have the tiny drill bit or small drill motor. I only had a hacksaw, so I simply made two cuts, opposite each other in the interior lift pipe. The cut was made the single thickness of the hacksaw blade and about 1 inch above the bottom opening of the larger exterior pipe (Figure 3A).”
It turns out that when the compressor is turned on, that the water between the outside casing pipe and the interior lift pipe is “pushed down” until it reaches the two opposing slits in the interior pipe. The air enters each slit (directly opposite each other) and literally cuts the water like a knife. After cutting the water, the air burst rises upward, lifting the water in the interior pipe all at once. This slug of air lifts all of the water in the interior pipe and comes out as one slug of water. After that first burst of air releases, thus clearing the interior pipe of water, additional water rushes in to fill the bottom of the ‘pipe-in-a-pipe’ pump. Once moving, the water in the interior pipe is 50% air and much lighter, so the air compressor has an easier time pumping the water.
The inner pipe is open to the source water and is cut at an angle to prevent it from being completely blocked (Figure 3B.). The bottom space below the two air slits and between the inner and outer pipe can be sealed without the use of the coupling and bushing pictured here (e.g. with a fabricated plug) but this method is convenient if the parts are available. With this approach the inner “stop” on the bushing has to be filed away to allow the inner pipe to slide all the way through while still preserving an airtight seal. The same goes for the other bushing at the top of the outer pipe.
Application for Small-Scale Aquaponics
A typical application of the airlift pump, as is the case at our Natural Farm Training Center in Hawaii, requires lifting 500 to 1000 liters of water per hour, available for gravity flow through an aquaponics system (Figure 4). In this case, the airlift pump is an excellent option, aerating the water as it is lifted into the tank above. We have labeled this set up for better understanding of the practical arrangement of the various airlift pump components
This airlift is pumping about 900 liter/hour from an IBC tank to a height of 1.8 meters to a clarifier. The vertical 3-inch PVC pipe is fed water by a ‘T’ connection to the IBC tank (Figure 3). This 3 inch pipe has a cap on the bottom and serves as a kind of ‘sump well’ for the actual ‘pipe-in-a-pipe’ pump. This well pipe, with the ‘pipe-in-a-pipe’ airlift inside, extends 80 cm below ground level (1.5 meters depth would have been better as the volume output of the pump would have increased and we could probably have used a smaller air compressor). The airlift itself is made from a 2-inch outer pipe and a 1.25-inch inner pipe. Water is pumped up and diverted into the tank while air exits out the top.
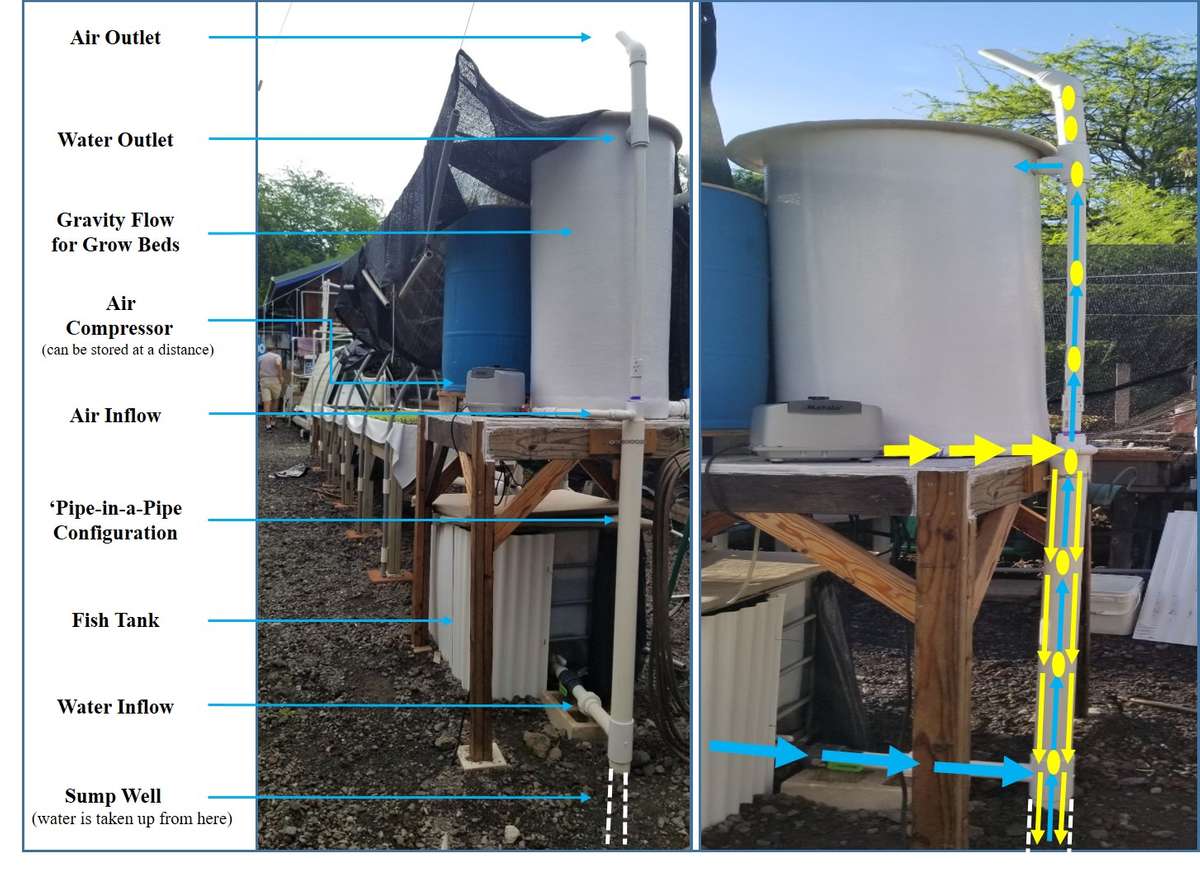
Acknowledgements & References
Many thanks to Glenn and business manager Natalie Cash for the generous contributions of time, tools, and materials for our teaching program at the Natural Farm Training Center, Science & Tech Dept., YWAM, University of the Nations. We are also grateful for your willingness to share these findings with ECHO and its Network around the world.
Martinez, G. Olomana Gardens Aquaponics Manual. available: https://www.olomanagardens.com/shop/aquaponics-manual/