We share many ideas in EDN for agricultural techniques that can increase crop production. Higher production translates into more food and potentially more income; this is very important, especially for farmers whose livelihood comes from a small piece of land.
Another way to increase food supply and income is to minimize post harvest losses. These losses—due to insects, rodents and fungi—are often reported at 30 to 50 percent or even higher.
Post harvest losses can be minimized through practices that improve grain storage, such as the use of metal silos. We learned about the widespread promotion of metal grain silos in Central America in the late 1990s. Just recently, I noticed reference to metal grain silos in Spore magazine, issue 152 (http://spore.cta.int/; available in English, French and Portuguese). The Spore article reported that the silos are now being successfully introduced in eastern Africa. Postcosecha (meaning “after the harvest”), the organization that introduced metal grain silos to Central America, is now helping facilitate introduction of the silos in Africa, supported by CIMMYT (International Maize and Wheat Improvement Center) and the Swiss Agency for Development and Cooperation (SDC).
Airtight construction is the key to success with metal grain silos. Galvanized sheet metal is cut using patterns, then soldered together to make the silos airtight. Dry grain is placed in a silo, which is then sealed and fumigated with phosphine tablets (available under many trade names, including phostoxin, gastion, detia, quickphos or celphos). Because the tablets are toxic they must be wrapped (for ease of later disposal) before they are placed on the surface of the grain. After ten days, fumigation is complete. The grain can be eaten one day after the end of the fumigation period. Properly stored grain can be stored for over a year. Grain is accessed from a spout at the bottom of the silo (Figure 1).
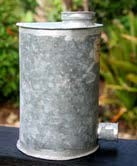
Metal grain silos are relatively inexpensive, but there is an upfront cost. Last year in Homa Bay, Kenya, a silo that stored three bags of grain cost around US$74. A silo that stored 20 bags of grain cost around $350. The cost can be recouped fairly quickly. According to the Postcosecha website, “With the Postcosecha technology, farmers in Central America typically are able to pay off their initial investments of 30 to 100 USD within one or two harvest cycles, while benefits last for 15 to 20 years.”
Introduction of the silos seems to work best with the involvement of NGOs (to coordinate and possibly arrange for micro loans), tinsmiths (to build the silos locally; one for every two thousand families that are potential silo users), farmers (who purchase and use the silos) and extension agents (to train farmers and tinsmiths). To this end, Postcosecha’s website (www.postharvest.ch) features publications (see examples below), targeted to:
- Organizations such as NGOs: “Getting to Know the Metal Silo”;
- Extensionists: “Metal Silo–Handling Stored Grain”; also “Salt method to determine moisture contents in basic grains”;
- Tinsmiths: “Technical Manual for the Construction of Small Metal Silos”;
- Farmers: (the documthe document available on the website only shows up in Spanish).
These documents can be downloaded free of charge. The site also contains a preview of a comprehensive document entitled “Manual for Manufacturing Metal Silos for Grain Storage.More information is online at www.postharvest.ch/en/Home/Documentation/
Tinsmiths, typically local artisans, are essential in silo promotion. Silos can be made on site.
David Balsbaugh, a former ECHO staff member, traveled in Central America in the spring of 2000. He later shared,
“I had the privilege of spending a week with a long-time farming couple from the USA, Benjie and Merrill Esch of Agape Ministries in Honduras. Merrill, is [also] skilled in appropriate technology. What caught my attention the most [among the projects I viewed] was the grain storage project, and particularly how the people of this rural Honduran community were so enthusiastically involved. Everywhere we traveled we saw neatly constructed grain silos near homes.”
Merrill gave a presentation on metal silos for grain storage at ECHO’s Agricultural Conference in 2000. The silos are like a big tin can, and can hold up to 1800 pounds of corn (enough to feed an average family for three to five months). Corn must be shelled before storage, but it often has to be shelled before it is marketed anyway.
Merrill gave several helpful tips regarding grain storage:
Check the market before investing in infrastructure for grain storage. In Honduras, it made sense to invest in the infrastructure. In 2000, Merrill shared that farmers were paid 90 lempiras for 100 pounds (45 kg) of corn right after harvest. Later in the year, if they needed to purchase corn, it cost 300 lempiras to buy that amount of corn back. In addition to protecting the grain, metal silos offer food security to farmers and the community, making them more independent of markets.
A sustainable program must be locally operated. Merrill commented that the money to promote grain silos in Honduras was provided by a non-profit organization from Europe. At first silos were given away—but funds were misused, and people who were given a silo were the most likely to fail with it. Instead, a loan program was set up in the community to help with purchase of the silos. (In the later years of the project, Merrill commented that they did not extend credit to anyone. At harvest time, the farmer could sell enough corn to buy a silo and then store some of the crop for later sale.)
Tinsmiths/artisans must be skilled and properly trained to manufacture quality silos. One tiny hole or an improper solder joint would render the silo inoperative. Silos should be made right in the community. Making silos is a great business opportunity that does not require electricity or much investment in tools or overhead expenses. The grain MUST be dry before being stored in a metal silo! To check for moisture in corn, heat sea salt in a pan on the stove at low heat and stir until dry. Mix 15 ml (1 Tbsp) salt and 475 ml (2 cups) of corn in a jar. Seal and shake it, then let it set overnight. The next day, shake the jar; if salt sticks to the glass, the corn kernels are not yet dry enough.
Stories from Central America
A few case studies illustrate how life-changing these metal grain silos can be. In 2006, Merrill and his wife Benjie shared encouraging stories about the continued use of metal grain silos in Honduras (see below). They commented,
“In our experience the use of the metal grain silos was a very liberating thing for Honduran Farmers. It was wonderful to have a small part in helping farmers to get out of debt and be more in charge of their own destinies. We saw widows who, for the first time, with the aid of a silo could feed their families from harvest to harvest without going hungry.”
Miguel. The Esches shared, “Miguel was part of a farmers’ co-op in Canchis and farmed about 4.5 to 5 acres (1.8 to 2 hectares). He started out with two silos which held 818 kg (1800 pounds) each. This was enough to carry him from one harvest to the next. (A family of 10 with teenage boys can eat 34 kg (75 pounds) of corn a week, made into tortillas.) Every year he borrowed about US$75.00 in order to buy fertilizer and herbicide and to pay some men to help him plant, as he also was a pastor of the local church.
“Several years ago, the man he usually borrowed from demanded the papers to his home for security. He knew better than to give him those papers and came to us for a loan. At that point we didn’t have the money to loan but a work team was visiting and they took up an offering and asked Pastor Miguel to put that money in the bank after every harvest so he never would have to borrow the money again.
“Well, by harvest time another group had given money so that all the pastors in our pastors’ association could receive a silo. Thus, Miguel now had three silos. He…use[d] the third silo to store corn in place of putting the money in the bank. A silo full of corn at planting time that year was worth about US$450.00 and at planting time he could sell some corn from that silo to buy fertilizer and herbicide. He could also then pay his workers with corn. This is a common practice, because the price of corn is always very high at planting time and people are glad to work for a payment in corn. A day’s wage then was about $2.25 and equal to about 12.5 pounds of corn. Most years at planting time, 25 pounds of corn was equal to two days’ wages. At that harvest time, the workers said to Miguel, "Be sure and fill your extra silo with corn so you have it to pay us next planting time.” To our knowledge, Miguel has not gone into debt since to plant his corn.”
Pastor Liberato. “Pastor Liberato has a large family, so he had four silos. When his father was sick in the hospital and then died, Liberato was able to sell a silo full of corn to pay for transportation and the expenses of the funeral without going into debt. He has since been able to purchase about six acres of land and so can plant more corn. He now has five silos. It is better than money in the bank, because when the farmer can wait from harvest until almost planting time to sell, he gains far more than the bank pays in interest. At harvest time the farmer usually gets $9-10 per 100 pounds of corn. At planting time he gets $23-25 (or more) per 100 pounds.”
Don Francisco. “Don Francisco had bought a silo every year at harvest time for five years. He was a very hard working man. .By selling 600 pounds of corn (more or less) at harvest, [Don could purchase a silo (at a cost of $56) and then] store 1800 pounds to sell at planting time for $450.00.”
Stories from East Africa
An article on the CIMMYT website shared a few stories of lives in Africa that have been changed because of metal grain silos. In Kenya, Sister Barbara Okomo, principal of a girls’ secondary school, has 10 metal silos at the school. She is quoted in the article: “I have used the silos for several years now, and I am convinced that this is the best method to store grain. With other storage methods, we would lose up to 90% of our stored grain—now we lose nothing.”
Conclusion
In East Africa and Central America, metal grain silos have successfully curbed post-harvest losses and given farmers greater food security. Detailed information about this technology is available from Postcosecha. As always, we would appreciate hearing of experiences with this technology if you give it a try.
Links for more information
View a news feature on metal silos, aired in Kenya. www.ntv.co.ke/News/Food%20security:%20Preserving%20grains%20in%20metalic%20silos%20/-/471778/947114//e8n5gqz/-/index.html
To check for moisture in corn, heat sea salt in a pan on the stove at low heat and stir until dry. Mix 15 ml (1 Tbsp) salt and 475 ml (2 cups) of corn in a jar. Seal and shake it, then let it set overnight. The next day, shake the jar; if salt sticks to the glass, the corn kernels are not yet dry enough.
Cite as:
Berkelaar, D. 2011. Metal Silos for Improved Grain Storage. ECHO Development Notes no. 112